Tungsten Manufacturing Operations
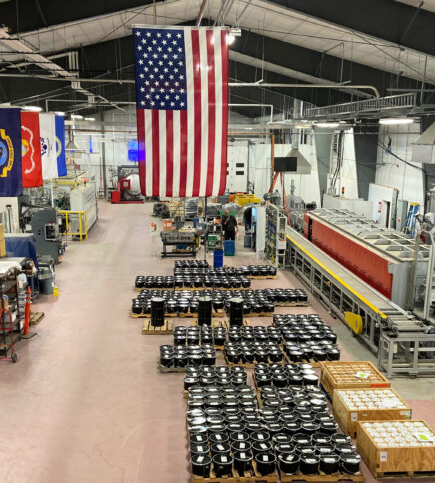
Requirements to Produce our Quality Certified Tungsten Products; tungsten ball, tungsten, sphere, tungsten cube are:
- People: Metallurgical, Mechanical, Chemical, and Industrial Engineering staff coupled with Technical Operators and Machinists.
- Equipment: Customized. High-Tech Machinery and Systems.
- Processes: Fully Integrated Chemical, Mechanical and Industrial Manufacturing Processes.
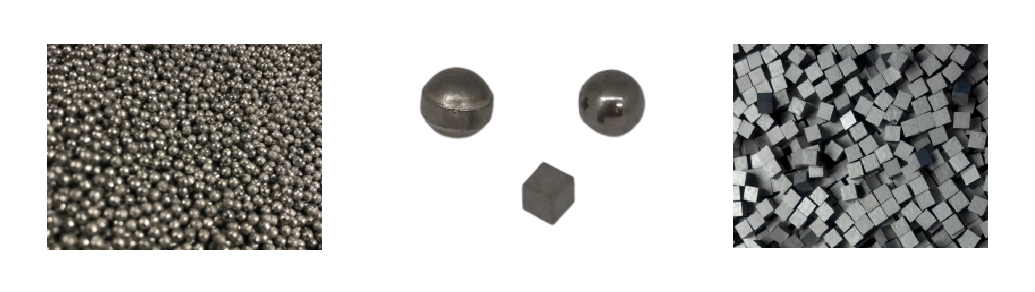
Tungsten Manufacturing Operations
At Tungsten Parts Wyoming, we specialize in the precision production of high-performance tungsten components. Our tungsten manufacturing operations are engineered to meet the most demanding requirements across defense, aerospace, automotive, energy, and medical sectors. With a strong focus on quality, consistency, and innovation, we produce tungsten balls, tungsten spheres, and tungsten cubes with unmatched density, precision, and metallurgical integrity.
Industry-Leading Tungsten Manufacturing
The manufacturing of tungsten products requires specialized knowledge and infrastructure. Tungsten’s unique material properties—including its high melting point, density, and hardness—demand specialized handling at every stage of the production process. At Tungsten Parts Wyoming, we employ a vertically integrated system that allows full control over each manufacturing step, ensuring reliability and repeatability.
Our process starts with the highest quality raw tungsten powder and ends with finished components that exceed industry standards for precision, purity, and performance.
Expert Personnel & Engineering Oversight
Every successful tungsten product begins with the people behind it. Our multidisciplinary team of engineers and technicians brings together decades of collective experience in:
-
- Metallurgical Engineering: Overseeing alloy formulations and heat treatments.
- Mechanical Engineering: Designing custom tooling and press operations.
- Chemical Engineering: Monitoring purity and managing binder chemistry.
- Industrial Engineering: Streamlining workflows to maximize efficiency and consistency.
We complement our engineering leadership with highly trained technical operators and machinists who understand the precision required for working with tungsten materials. Our team operates under a company-wide culture of continuous improvement, safety, and accountability.
Step-by-Step Tungsten Manufacturing Workflow
Our tungsten production process is carefully structured to ensure high-quality results with minimal variation. Each phase is monitored for compliance with quality standards and customer-specific requirements.
1. Powder Receiving & Quality Testing
-
- All incoming tungsten powder is tested for particle size, flow characteristics, composition, and density.
- Our internal lab validates powder quality before it enters production.
2. Powder Compacting
-
- Tungsten powder is formed into green shapes using high-pressure compacting techniques.
- A proprietary binder is used to hold the shapes together during initial handling.
3. Debinding
-
- Compact forms are subjected to a controlled thermal environment to remove all binding agents without distorting the shape.
- This process is critical for preparing the parts for densification.
4. Liquid-Phase Sintering
-
- The debound compacts are heated to near-melting temperatures in a carefully controlled atmosphere.
- Sintering transforms the powder structure into a dense, solid tungsten alloy, achieving the desired mechanical and physical properties.
5. Vacuum Annealing
-
- Final heat treatment is done in vacuum furnaces to relieve internal stresses and enhance material toughness.
- Vacuum annealing is essential for applications requiring superior mechanical integrity.
Post-Sintering Operations
Once the tungsten parts have undergone primary formation and heat treatment, they enter a series of precision finishing stages:
6. Tumbling & Grinding
-
- Tumbling polishes and smooths component surfaces.
- Grinding ensures products meet strict dimensional tolerances, especially for spheres and cubes.
- We maintain one of the largest grinding facilities in the U.S. for tungsten components.
7. Sorting & Sizing
-
- Parts are sorted by dimension, weight, and density.
- Sizing equipment, such as roller meters and calibrated measuring systems, is used to classify products.
8. Cleaning & Surface Treatment
-
- Ultrasonic and chemical cleaning remove any residual contaminants.
- This step is vital for customers in high-purity applications like medical and aerospace.
9. Quality Verification & Final Inspection
-
- A minimum of seven verification steps are required before any product leaves our facility.
- Inspection criteria include size, roundness, density, surface finish, and internal integrity.
10. Secure Packaging & Shipping
-
- Products are packaged in custom containers to preserve quality in transit.
- Orders are shipped worldwide with full traceability and compliance documentation.
Certifications & Compliance
Our tungsten manufacturing operations are governed by strict internal and external quality systems. Tungsten Parts Wyoming is certified to industry-standard quality management systems, and all products can be produced to comply with:
-
- ISO specifications
- ITAR and DFARS sourcing requirements
- Military and aerospace specifications
- ASTM material standards
We work closely with clients to ensure every shipment meets the required documentation, traceability, and compliance expectations.
Why Choose Tungsten Parts Wyoming
When you choose Tungsten Parts Wyoming, you’re not just purchasing a product—you’re gaining a strategic manufacturing partner. Here’s why global leaders trust us with their tungsten component needs:
-
- Vertically Integrated Production: We control the entire process, reducing supply chain risks.
- Custom Solutions: Whether it’s a proprietary alloy blend or a specialty shape, we can develop tungsten products tailored to your application.
- Precision at Scale: Our facility can support both high-volume production and small-batch custom runs with the same attention to quality.
- U.S.-Based Operations: All manufacturing is conducted in the United States, ensuring geopolitical security and fast turnaround.
Applications of Our Tungsten Products
Our tungsten balls, spheres, and cubes are used across critical sectors:
-
- Defense and Munitions: For armor-piercing projectiles and counterweights.
- Medical Imaging and Radiation Shielding: Due to tungsten’s high density and shielding properties.
- Aerospace: For balance weights in satellites, helicopters, and missiles.
- Industrial Machining: As precision counterbalances and wear-resistant tooling.
- Electronics and Energy: In applications requiring high thermal stability and conductivity.
Incoming Powder Receiving & Testing
Fette-Powder Compacting
De-Binding
Sintering
Tumbling
Annealing
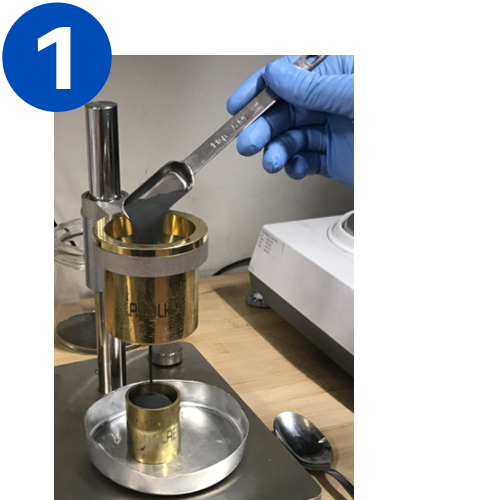
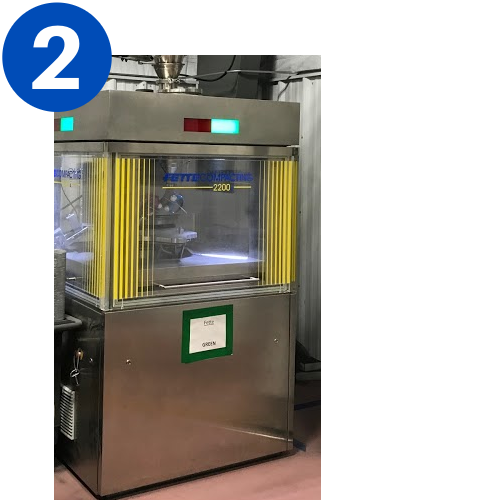
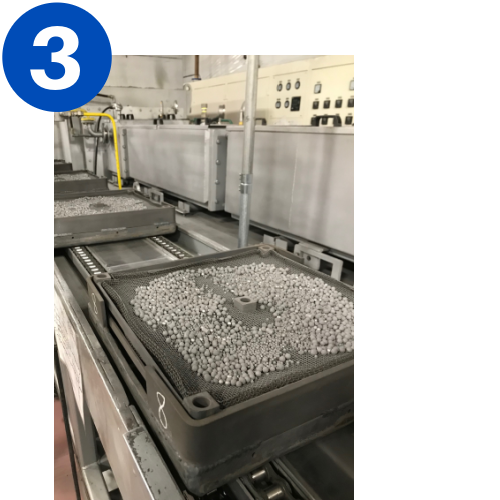
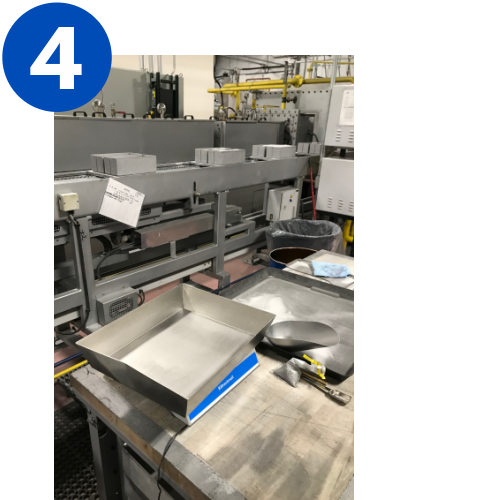
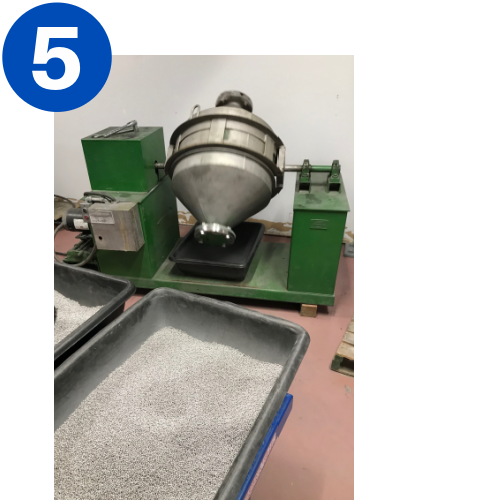
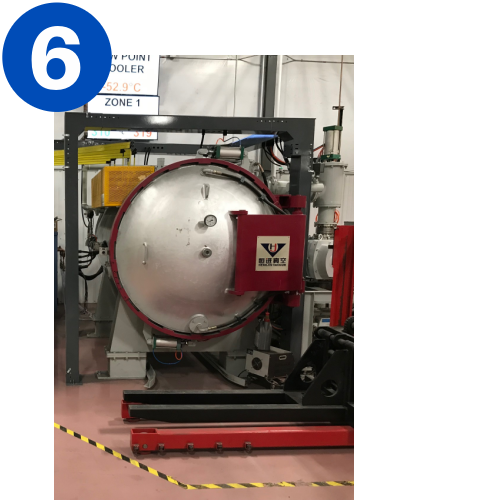
Sorting
Grinding
Cleaning-Washing
Sizing-Roller Meter
Quality Testing
Shipping
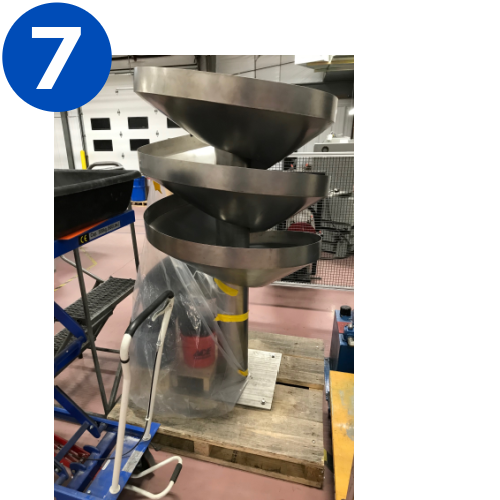
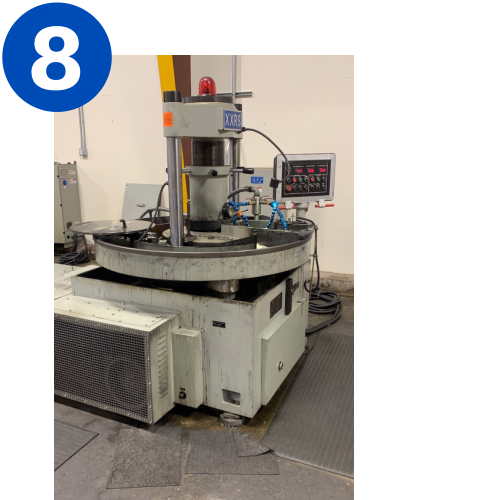
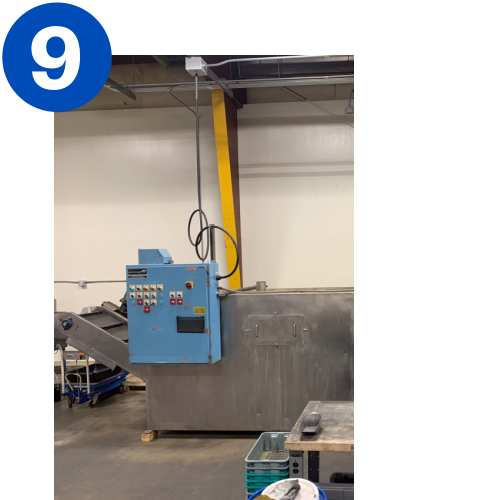
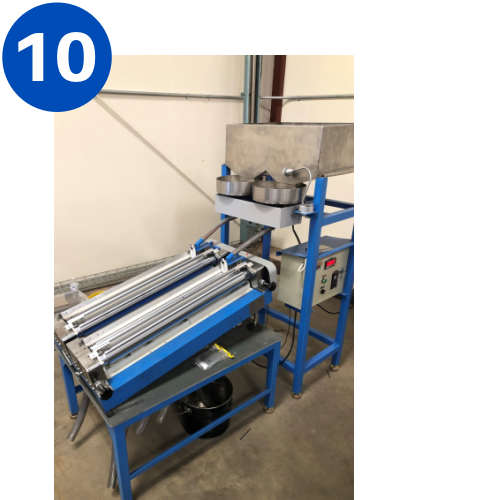
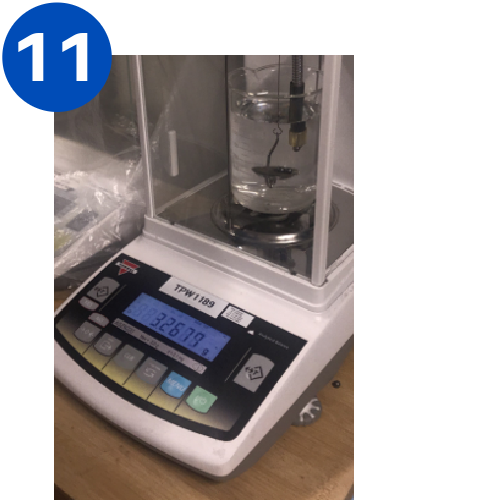
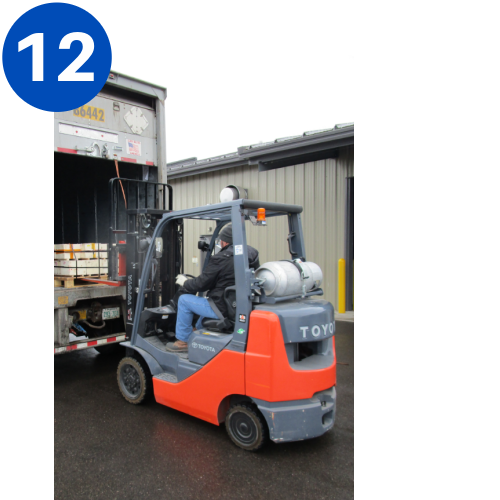