What is Tungsten
Tungsten is an element with an atomic number of 48 on the periodic table. It is metallic, like iron, aluminum, copper, etc., but possess some very special properties:
- It has a very high density (19.2 g/cm3), higher than all other elements except platinum, osmium and iridium – all which are more expensive and rarer.
- It has the highest melting point of all know elements – 3422oC (6192 oF)
- It is the strongest natural metal pure metal, with the highest tensile strength of any pure metal – 980 MPa or 500ksi.
- It is very hard, up to 9.0 on the Moh’s hardness scale, with 10 being diamond.
- It has the lowest vapor pressure of all metals – meaning that it is very resistant to evaporation/sublimation at high temperatures.
- It is resistant to corrosion and oxidation.
- Low coefficient of thermal expansion – 4.4 x 10⁻⁶ m/m/°C (dimensions change less with temperature change compared to most metals).
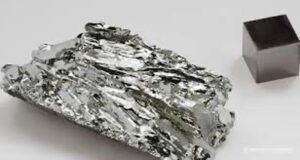
Elemental Tungsten
Applications of Tungsten
The properties of tungsten makes it useful, by itself, or combined with other elements in applications that require density, hardness and/or resistance to temperature, including:
- Aerospace and Defense (penetrators, projectiles, armor piercing rounds, counterweights)
- Manufacturing/Construction/Mining (drilling, machining, sawing, bucking bars)
- Radiation Shielding
- Electrical (bulb filaments, vacuum and x-ray tubes)
- Welding (Electrodes)
- High Temperature (heating elements)
Tungsten’s Occurrence in Nature and Mining
Tungsten is a somewhat rare metal in the earth’s crust, with an abundance of about 1.5 parts per million. Although not as common as iron or aluminum, it occurs about as much as does tin and is more than 500x more abundant than gold. Tungsten does not occur as a pure metal in nature, but as minerals such as scheelite (CaWO4) and Wolframite (Fe, Mn) WO4) which are the two most commercially important sources for tungsten.
![]() Wolframite |
![]() Scheelite |
Tungsten, in mineral form, is not distributed uniformly over the world. More tha 50% of current reserves are in China, followed by Russian and Vietnam (Merchant Research & Consulting Ltd., 2025). Only a small fraction of reserves are in the United States:
The impact of China on tungsten production is even more. Over 80% of global tungsten production is controlled by China. However, China has now placed export controls in place, creating market volatility and increased tungsten prices, creating new opportunities for production. No American-made tungsten has been mined since 2016 (US Department of the Interior and U.S. Geological Survey, 2017)due to Chinese dominance and cheaper tungsten sources outside of the USA. Because of security concerns (Chinese will be banned in 2027 in the USA for military applications of tungsten for aerospace and defense ), there are projects underway for us made tungsten as well as other countries such as South Korea, Spain, Australia to bring more production outside of China online (Tungsten Metals Group LTD, 2024). Tungsten Parts Wyoming is already only using tungsten produced outside of China.
Tungsten Production Process
Tungsten ore or Tungsten scrap can be used in tungsten fabrication. The first step is to create an intermediate product ammonium paratungstate (APT) [(NH4)10[H2W12O42]·4H2O], that is a powder containing 88% WO3, as an intermediate product. APT is then thermally decomposed to create tungsten yellow or blue oxide, depending on if oxidizing or reducing conditions are present. which can then be reduced with hydrogen gas to make tungsten metal powder, which can then be used in creating tungsten metal and other tungsten-containing products such as cemented carbides.
Tungsten Production Process (International Tungsten Induatry Association)
![]() ORE Powder |
![]() APT |
![]() WO3 |
![]() Tungsten Powder |
From Powder to Dense Shapes
Because of the very high melting temperature of tungsten, it is not practical to make products through melting and casting such as done with common metals such as steel, aluminum, copper, etc. Instead, a process called powder metallurgy is used. Tungsten powder and any desired alloying additions are mixed into the desired composition. The powder is pressed into a compact of desired geometry. It is then heated to 1800-2700 °C in a furnace, usually containing a hydrogen atmosphere to reduce oxides and promote thermal conductivity. At this very high temperature, the tungsten atoms become more mobile in the solid state and are capable of solid-state diffusion in which the powder particles join and fuse into a solid mass. The driving force for this is the reduction of surface energy associated with the very large surface area over the many small tungsten particle surfaces. By sintering the particles together into one solid continuous mass the total surface area is reduced, and the product is more thermodynamically stable. After sintering, an additional heat treatment is done (annealing) in a vacuum in inert gas to remove embrittling hydrogen gas left in the product from sintering and improve mechanical properties by relieving stresses from the sintering operation.
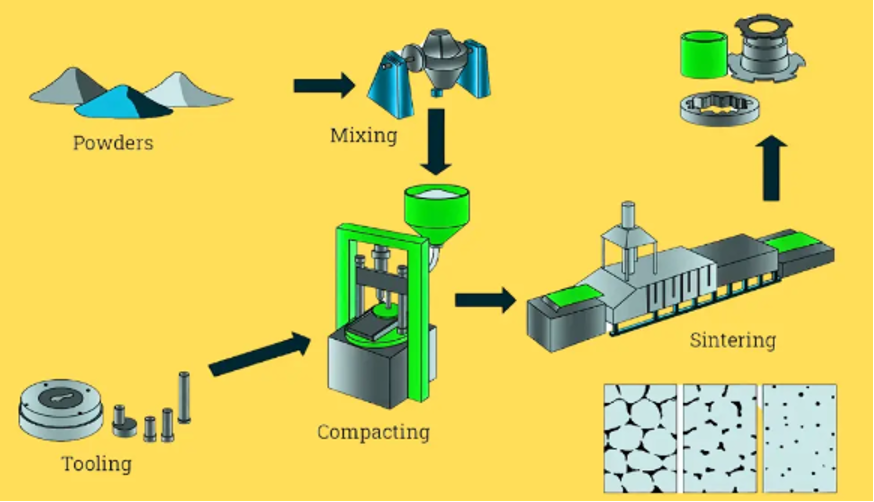
Stages of Powder Metallurgy (Sabihadiya)
Tungsten Heavy Metal Alloy (WHA): Improved Cost -Effectiveness and Superior Mechanical Properties
As mentioned, pure tungsten requires extremely high temperatures for sintering, requiring specialized equipment. In addition, at room temperature, pure tungsten is brittle with low toughness and machinability. It was the need to improve tungsten machining that led to the development of tungsten heavy alloy (WHA), an alloy that preserves most of the high density of tungsten, while improving mechanical properties such as strength, ductility and toughness. At the same time, WHA is generally easier to sinter thanks to the application of a phenomenon called liquid-phase sintering that allows for sintering at lower temperatures.
WHA is differentiated from tungsten by having up to 10% weight replaced by so-called matrix alloy elements such as nickel, iron, cobalt and copper These matrix alloy elements, when combined with tungsten form, during heating, what is called a eutectic consisting of tungsten and a liquid phase formed at a temperature (1400-1550 °C) that is significantly lower than the sintering temperature of pure tungsten (1800-2700 °C). Sintering in this liquid phase allows for full densification of WHA and results in tungsten equi-spherical grains surrounded by a matrix rich in the matrix alloying elements. The resulting solid is one that preserves most of the density of tungsten, but with improved mechanical properties such as ductility and toughness. As a bonus the matrix alloy elements are cheaper than tungsten and help to lower the cost of raw materials slightly.
![]() |
![]() |
Microstructures of pure tungsten (left-note porosity (Research Status of Manufacturing Technologyof Tungsten Alloy Wire, 2023)) and WHA (right).
WHMA Is divided by ASTM B777 into four classes:
Class 1 has the best machinability and ductility/fracture resistance. Class 1 is used when precision machining is required for complex counterweights for aircraft or difficult radiation shielding geometries.
Class 2 offers a balance of density, stiffness and toughness and is used for aerospace balance weights. Class 1 and 2 are both used for kinetic energy armor penetrators for military applications, when ductility (toughness) is needed to avoid fragmenting on impact with armor.

Examples of WHA Tungsten Spheres and Cubes Manufactured by Tungsten Parts Wyoming
Class 3 WHA is applied where heavier density is required but toughness is not as important in applications such as shot for turkey and water-fowl shooting. The high density makes it a non-toxic replacement for lead or steel shot, but with greater range.
Class 4, with the highest density (18.25-18.85) is used for the most demanding x-ray and radiation shielding applications.
Tungsten Parts Wyoming can produce all classes of WHA.
Non-Toxic Substitute for Lead
Previously lead was the go-to metal of choice for radiation shielding, commercial shot, and weights. However, as well publicized, lead was found to be toxic and has now been Because of their high densities that surpass that of lead (11.34), Since 1991, lead shot has been banned in the USA since 1991. Absorption of lead by humans has been shown to lead to damage to the brain, nervous, and reproductive systems and increase blood pressure. In addition, it is persistent in the environment, not easily degradable and leads to loss of biodiversity. Governments and organizations worldwide are limiting the use of lead increasingly and are pushing towards lead-free alternatives such as tungsten heavy metal to replace lead in areas such as shot and radiation shielding.
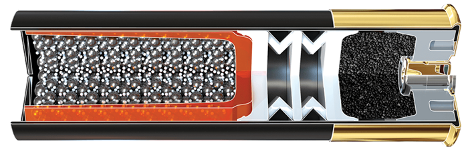
Winchester TSS Ammunition with Tungsten Shot
Future of Tungsten
As the US government increases its preparedness for future conflicts, the demand for “Made in USA tungsten “will grow. Similarly, as the pressure to increasingly replace lead with non-toxic material in areas such as hunting shot and radiation shielding for future green energy nuclear energy production, more tungsten will be used. Indeed, the tungsten market is predicted to increase considerably over the next years, growing from %5.66 billion in 2024 up to $8.92 billion. Thus, tungsten will play a stronger role in supporting the world to come., with Tungsten Parts Wyoming leading the way as a U.S. tungsten manufacturer.